- Messages
- 17,712
- Location
- Maryland
The Use of Specialized Hydraulic Presses in Stiff Felt Production
This excerpt is from "25 Berlin - Gubener Hutfabrik (Hat Factory), Actiengesellschaft (Public or Private Company) vorm. A. Cohn, Guben, 1913". It explains the use of special Hydraulic presses in Stiff Felt Production. This very important specialized process is no longer used in Stiff Felt production.
Up to this point, the felt stumps have traveled in closed batches from the spinning mill with a card containing all the necessary information through the raw manufacturing process. From the warehouses, they move on, separated according to individual commissions and divided up for the final shape. The felt stumps for Stiff Hats go to the Stiff Hat department, those for Soft Hats to the Soft Hat department.
If we first follow the former, we see how the felt stumps are soaked with a solution of shellac and spirit, then dried and later subjected to a washing process which is intended to remove the superfluous stiffness from the surface so that only the stiffness remains inside the felt. This washing process, called panning, is of utmost importance, because if the shellac is not completely removed from the surface of the stump, it will show up as mold-like stains when the hat is worn and even when it is stored.
The stiffened felt stumps are now fitted to the head shape for which they are intended, "plated", the edge is stretched flat and the hat is then pressed after its surface has been finely cleaned and brushed (see first photo below).
During the plating process, the felt stump is given the head shape that it should have in the finished hat - at least approximately. The stiff hat is only given its exact shape in the hydraulic press (see second photo below).
The hydraulic press consists of an iron frame, the lower part of which holds an iron mold, the cavity of which resembles the shape of a hat. This mold is polished smooth on the inside and holds the hat. The upper part of the press is fitted with an elastic rubber body which fits into the iron mold.
After the stiffened felt hat body has been heated in a box heated by steam or gas - which makes the shellac stiffness supple - the upper part of the press is lowered and the elastic rubber body is inserted into the hat. The press is then hermetically sealed and water pressure of 25-30 atmospheres generated by accumulators is let into the interior of the press through a pipe. The water fills the hat bag with this enormous pressure, expands it and this forces the supple lump to fit smoothly against the walls of the iron mold.
PLATING THE STIFF HATS
PRESSING THE STIFF HATS (WITH HYDRAULIC PRESSES)
This excerpt is from "25 Berlin - Gubener Hutfabrik (Hat Factory), Actiengesellschaft (Public or Private Company) vorm. A. Cohn, Guben, 1913". It explains the use of special Hydraulic presses in Stiff Felt Production. This very important specialized process is no longer used in Stiff Felt production.


Up to this point, the felt stumps have traveled in closed batches from the spinning mill with a card containing all the necessary information through the raw manufacturing process. From the warehouses, they move on, separated according to individual commissions and divided up for the final shape. The felt stumps for Stiff Hats go to the Stiff Hat department, those for Soft Hats to the Soft Hat department.
If we first follow the former, we see how the felt stumps are soaked with a solution of shellac and spirit, then dried and later subjected to a washing process which is intended to remove the superfluous stiffness from the surface so that only the stiffness remains inside the felt. This washing process, called panning, is of utmost importance, because if the shellac is not completely removed from the surface of the stump, it will show up as mold-like stains when the hat is worn and even when it is stored.
The stiffened felt stumps are now fitted to the head shape for which they are intended, "plated", the edge is stretched flat and the hat is then pressed after its surface has been finely cleaned and brushed (see first photo below).
During the plating process, the felt stump is given the head shape that it should have in the finished hat - at least approximately. The stiff hat is only given its exact shape in the hydraulic press (see second photo below).
The hydraulic press consists of an iron frame, the lower part of which holds an iron mold, the cavity of which resembles the shape of a hat. This mold is polished smooth on the inside and holds the hat. The upper part of the press is fitted with an elastic rubber body which fits into the iron mold.
After the stiffened felt hat body has been heated in a box heated by steam or gas - which makes the shellac stiffness supple - the upper part of the press is lowered and the elastic rubber body is inserted into the hat. The press is then hermetically sealed and water pressure of 25-30 atmospheres generated by accumulators is let into the interior of the press through a pipe. The water fills the hat bag with this enormous pressure, expands it and this forces the supple lump to fit smoothly against the walls of the iron mold.
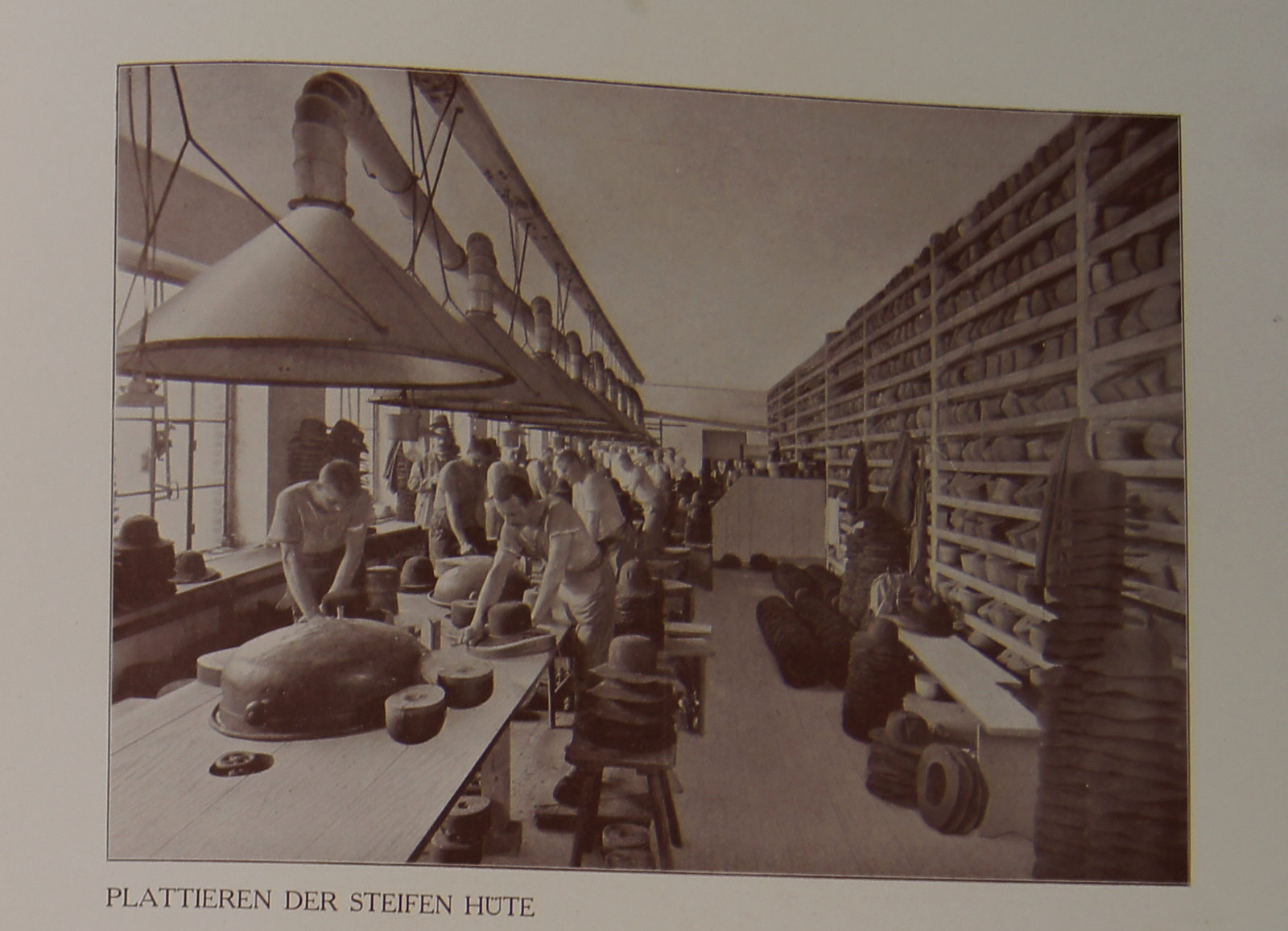
PLATING THE STIFF HATS

PRESSING THE STIFF HATS (WITH HYDRAULIC PRESSES)
Last edited: