- Messages
- 17,709
- Location
- Maryland
This is a visual tour of the Ebreichsdorfer Heimatmuseum (S. & J. Fraenkel Wien Hat Factory / Ebreichsdorfer Felt Hat Factory) which I visited March 10th 2017. I would to thank the Director of the museum Rudolf Dworak and his associates for showing me the museum during the off season and for putting me in contact with the last Director (started as Master Dyer in the mid 1950s) of the factory which closed in 1972. I would highly recommend visiting the museum if you are in the Vienna area. The town of Ebreichsdorf is located just south of Vienna.
https://www.heimatmuseum-ebreichsdorf.com/
S. & J. Fraenkel Wien Hat Factory / Ebreichsdorfer Felt Hat Factory produced both Felt and finished / semi finished Fur Soft Felt Hats. They were very well known for the fine Austrian Velours they produced going back to the late 19th Century (founded 1874). By the late 1950s S. & J. Fraenkel Wien Hat Factory / Ebreichsdorfer Felt Hat Factory was the largest Felt and Hat factory in Austria. They acquired the Brüder Böhm trademark and other trademarks of former Austrian Hat Factories. They also produced finished hats for Dunn & Co. of England among others. At the time of the factory closing in 1972 they were last large scale Felt and Hat factory in Austria.
I will start with Felt and Hat production section of the exhibit.
Part One
Click On Photos To Expand! (Recommended!)
The Hair Stump / Hood Production
From the Fur to the Stump / Hood, Cut Hair, Hair Mixing, Clean (Blow) Hair
Hare and rabbit hair are the raw material for felt hat production. In the past, hair from beaver, muskrat or otters played a certain role as additions. (left side caption)
In hairdressing the hair of the coat is separated on the skin, whereby the hair fleece as a whole is preserved ("kitten"). After your First World War, the hairdressing of the Ebreichsdorfer felt hat factory was abandoned and prepared fur was purchased. (upper left photo caption)
Functional diagram of the hair clipper. (upper left HM 18 photo caption)
In the mixing plant, the hairs of many animals and distinguished by different qualities are mixed in specific proportions in order to bring the raw material to a uniform quality. (upper right HM 18 photo caption)
Trimmed hair (mixed and blown) (left side caption HM 15)
The blowing machine is used last Cleaning and dusting the hair, but especially for sharply separating coarse hair (bristle, prickly hair) from the soft downy hair, which is the sole raw material for making hats. (right side caption HM 20)
This cleaning process is full in 5 to 9 consecutively coupled chambers, in which air currents and fast-running spiked rollers blow up the hair (= blow). Heavier hair (bristle, prickly hair)
collect on the ground. From the last blow chamber the hair falls completely cleaned and mixed in the form of a wide uniformly streaming in the ready transport car, which brings it to the Facherei / Folding Department. (right side caption HM 20)
Fache / Forming
Hair Forming, Felting, Fulling
In the specialized machine, arises by uniform distribution of a particular
Amount of hair on the tray bell the basic shape of the future Stumpens.
(See original box on the right in the corner!)
The compartment bell is perforated. The air is coming from inside the compartment bell
sucked off, creating a negative pressure, which in the compartment housing (= "Dome")
reaching hair adheres to the rotating tray bell evenly distributed.
In order to prevent this hair layer thus obtained from
pressure and opening the dome falls from the box, the hair is already sprayed
before with hot water, making a first, however, only loose
binding arises. (far left diagram caption)
Felting Department Personal (HM 42, HM 22)
Probably the most common and also the most complete walke / fulling machine is the Multiroller. There are several models here, those with 12, 19, 29 or 30 rollers. The felts graze through between the parallel arranged rotating and horizontally and vertically shifting rollers. They are exposed to a hot water flow, which accelerates the felting. The feeding of the multirollers with the wrought material is done by a continuous felt chain, which is created by superimposing the felts. The felts graze after leaving the machine (see 'Felting') and reintroduced to achieve uniform coverage on all sides. After about 20 passages, the walking / fulling is finished with the multiroller, which ..... (lower right corner caption)
In the following work-style felts - (tossing) walking / fulling, the hair is given a firmer cohesion by moisture, heat, movement, and pressure.
The structure of the hair is compressed more and more, the felt arises. (center diagram caption)
For felting several compartments (6-8) are wrapped in a cloth and this
Rolls rolled between rollers. After several roll movements each roll becomes
opened, the subjects laid in a different direction and rolled again. This
Shifting ("crossing") can not be done by machines, but only by hand
and normally happens 16 times. (center diagram caption)
Walking / Fulling - Multi Roller Machine (HM 23, HM 43)
Workers Cap (center caption)
Fulling, Brushing, Touring, Clipping
The stumps are loosely placed in the walker / fulling holder during "hammer walking / fulling" to expose them to a pushing pressure from two hammers. Thus, the felting takes place from all sides at the same time. The hammers are toothed and push the stumps a little further with each up and down excursion, so that the entire material to be drilled comes into direct contact with the hammers.
During processing, the stumps are constantly sprinkled with the Fulling water.
At higher temperatures felting occurs more uniformly and much faster. After the Hammering Walken / Fulling the stump has shrunk compared to the compartment to 1/8 and is dense and firm. (lower center diagram)
Centimeter measure to check the size of the stump.
Fulling Roll ("Fulling Beater")
Velour Stumpen / Hoods, Automatic Hot Wet Brushed (lower right corner)
https://www.heimatmuseum-ebreichsdorf.com/
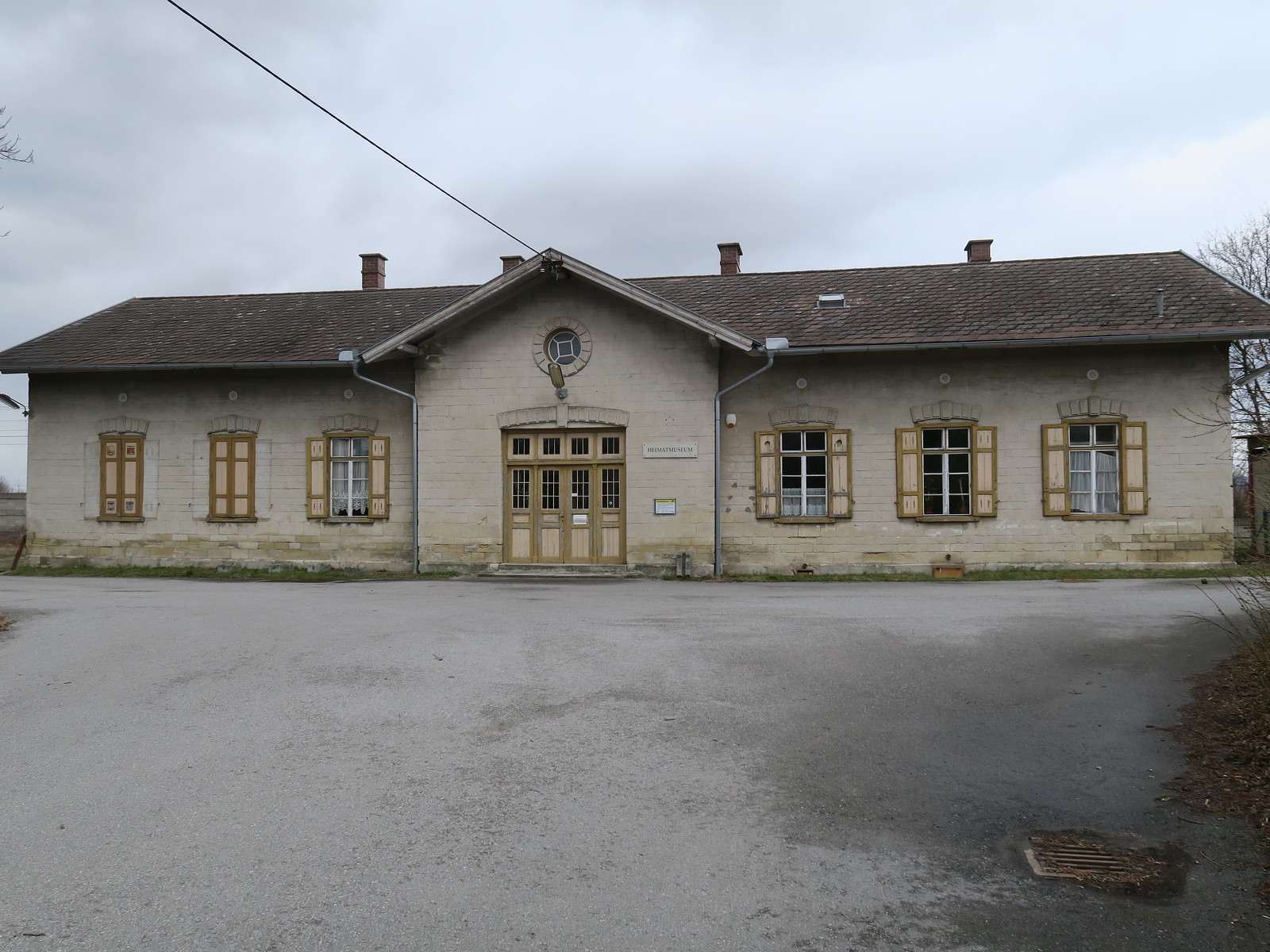
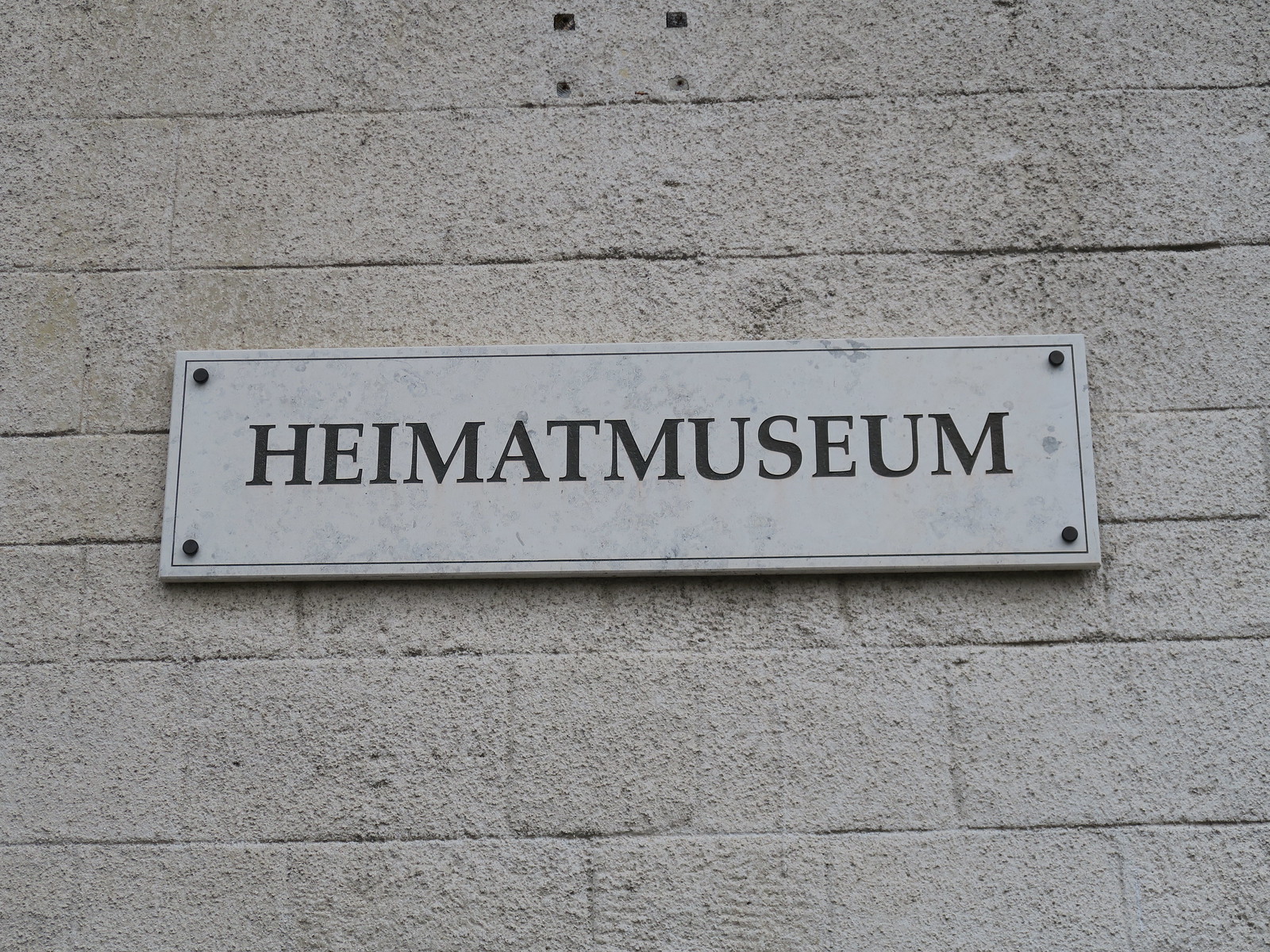
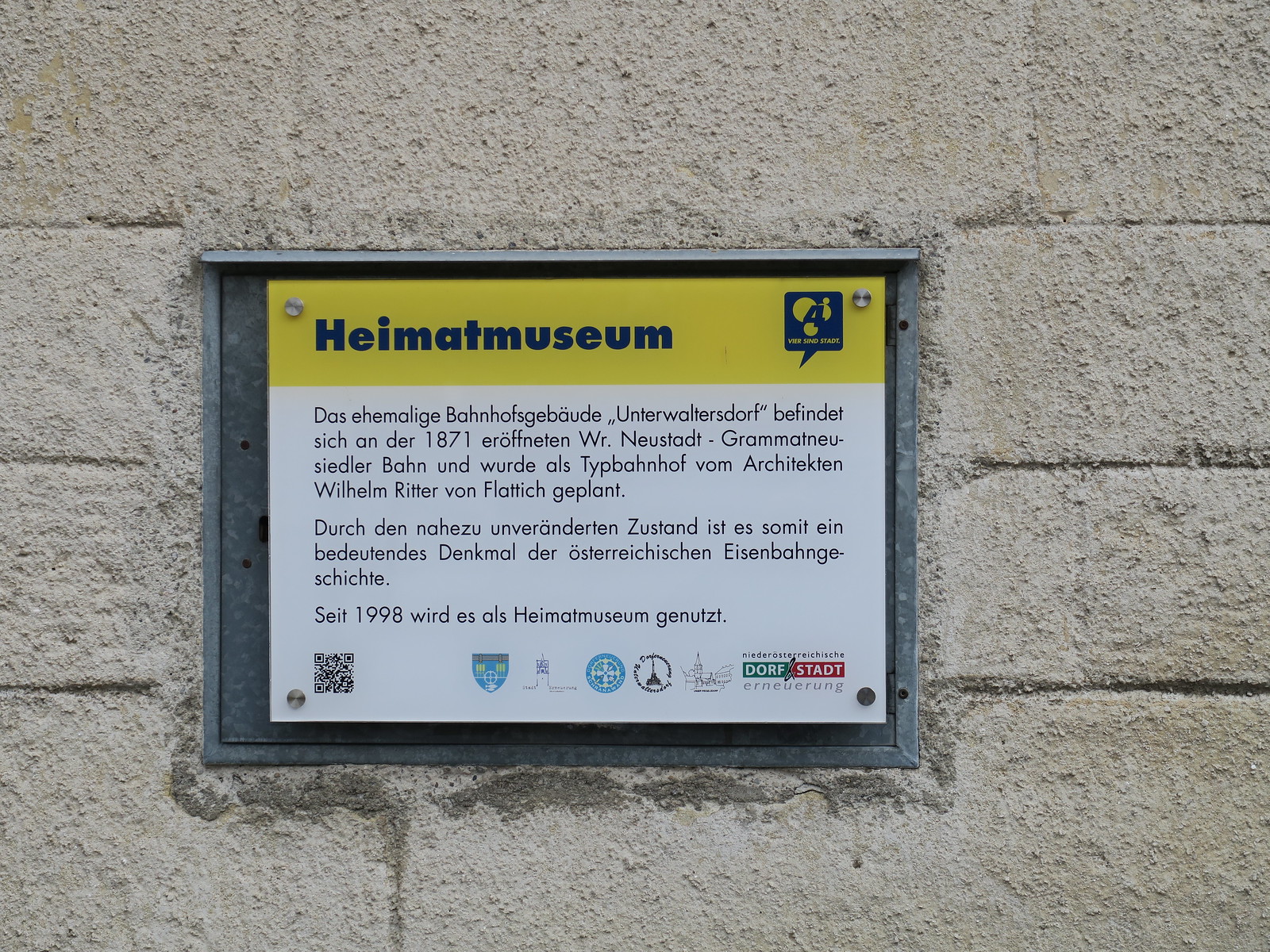
S. & J. Fraenkel Wien Hat Factory / Ebreichsdorfer Felt Hat Factory produced both Felt and finished / semi finished Fur Soft Felt Hats. They were very well known for the fine Austrian Velours they produced going back to the late 19th Century (founded 1874). By the late 1950s S. & J. Fraenkel Wien Hat Factory / Ebreichsdorfer Felt Hat Factory was the largest Felt and Hat factory in Austria. They acquired the Brüder Böhm trademark and other trademarks of former Austrian Hat Factories. They also produced finished hats for Dunn & Co. of England among others. At the time of the factory closing in 1972 they were last large scale Felt and Hat factory in Austria.
I will start with Felt and Hat production section of the exhibit.
Part One
Click On Photos To Expand! (Recommended!)
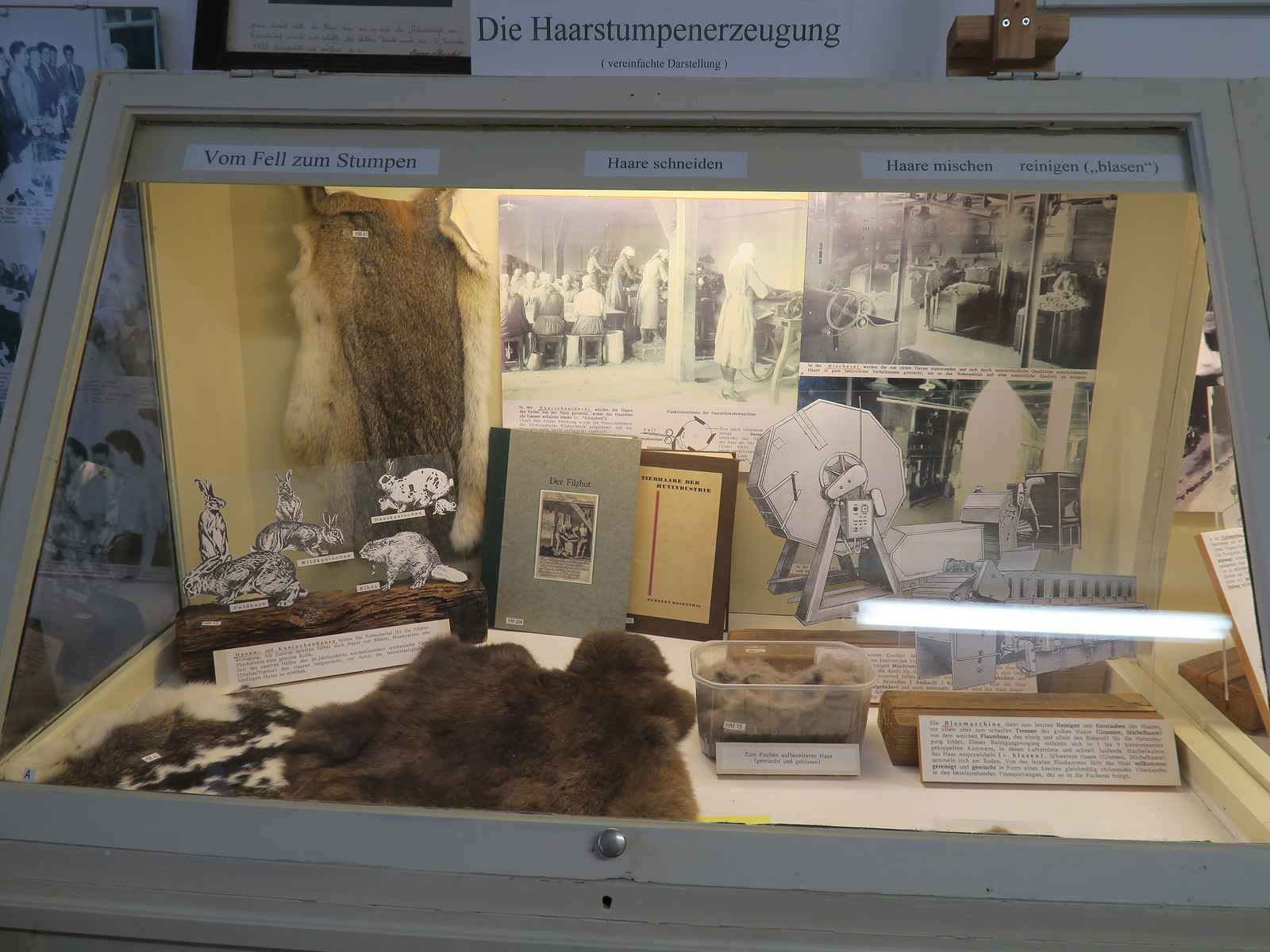
The Hair Stump / Hood Production
From the Fur to the Stump / Hood, Cut Hair, Hair Mixing, Clean (Blow) Hair
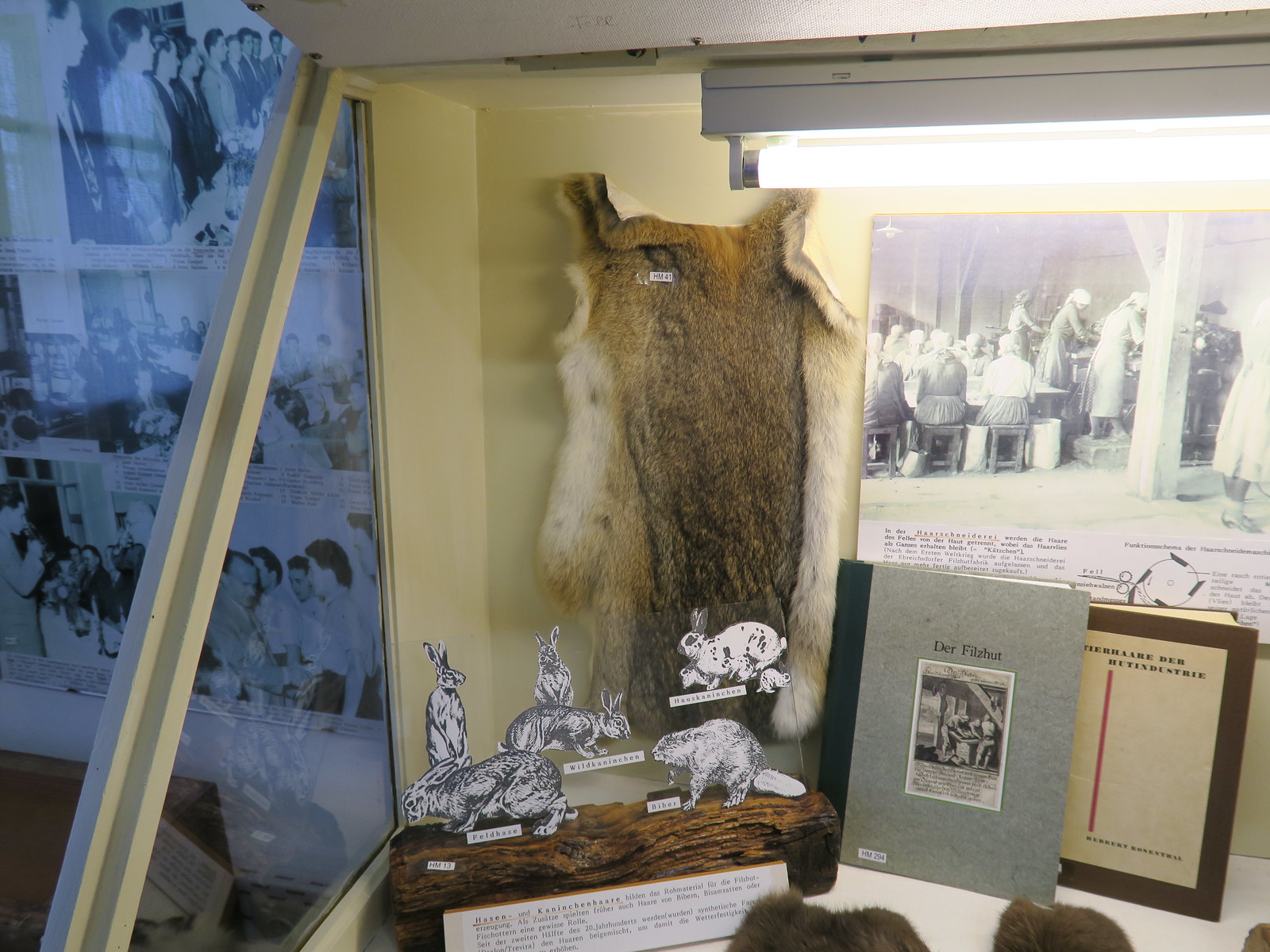
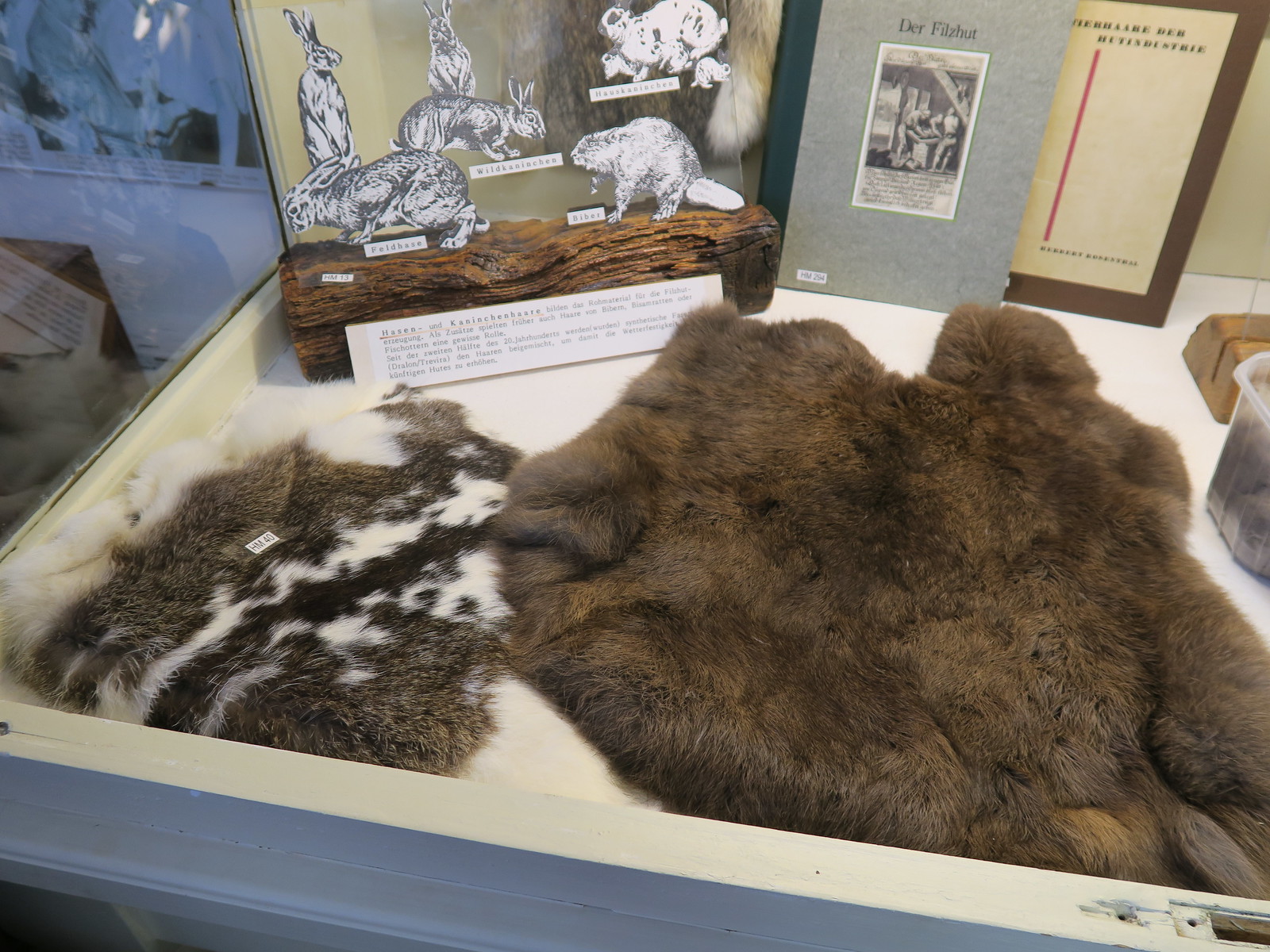
Hare and rabbit hair are the raw material for felt hat production. In the past, hair from beaver, muskrat or otters played a certain role as additions. (left side caption)
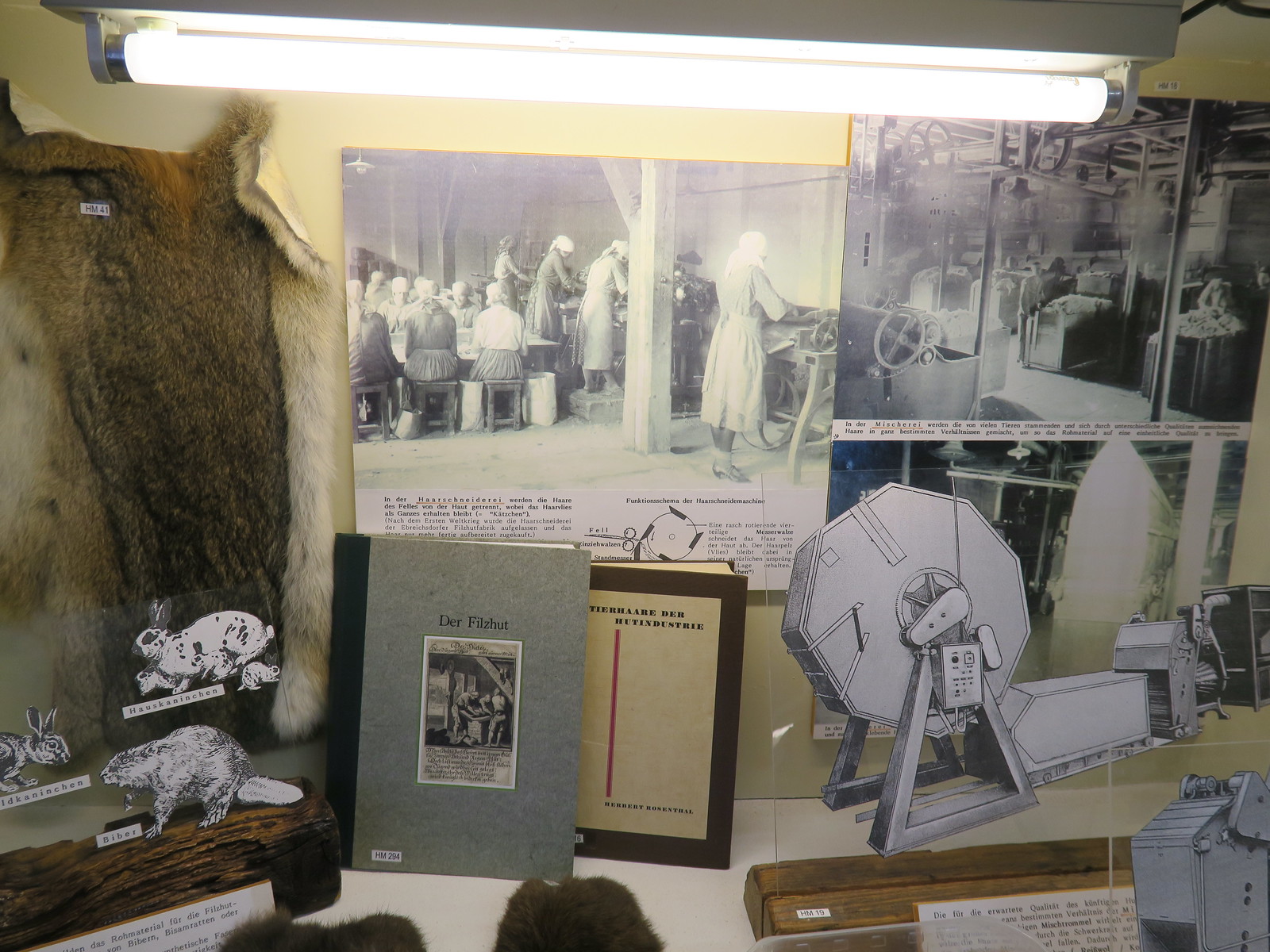
In hairdressing the hair of the coat is separated on the skin, whereby the hair fleece as a whole is preserved ("kitten"). After your First World War, the hairdressing of the Ebreichsdorfer felt hat factory was abandoned and prepared fur was purchased. (upper left photo caption)
Functional diagram of the hair clipper. (upper left HM 18 photo caption)
In the mixing plant, the hairs of many animals and distinguished by different qualities are mixed in specific proportions in order to bring the raw material to a uniform quality. (upper right HM 18 photo caption)
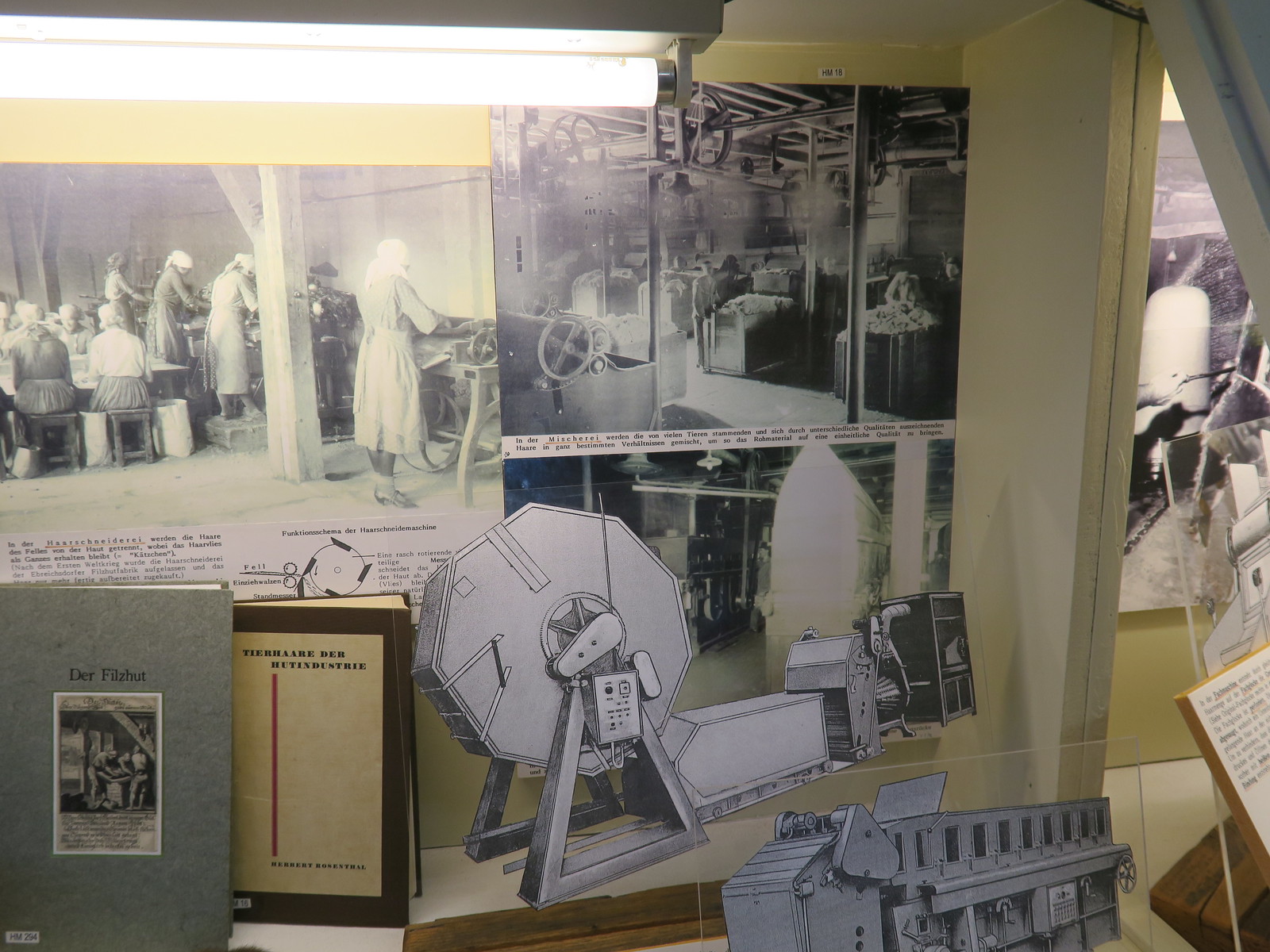
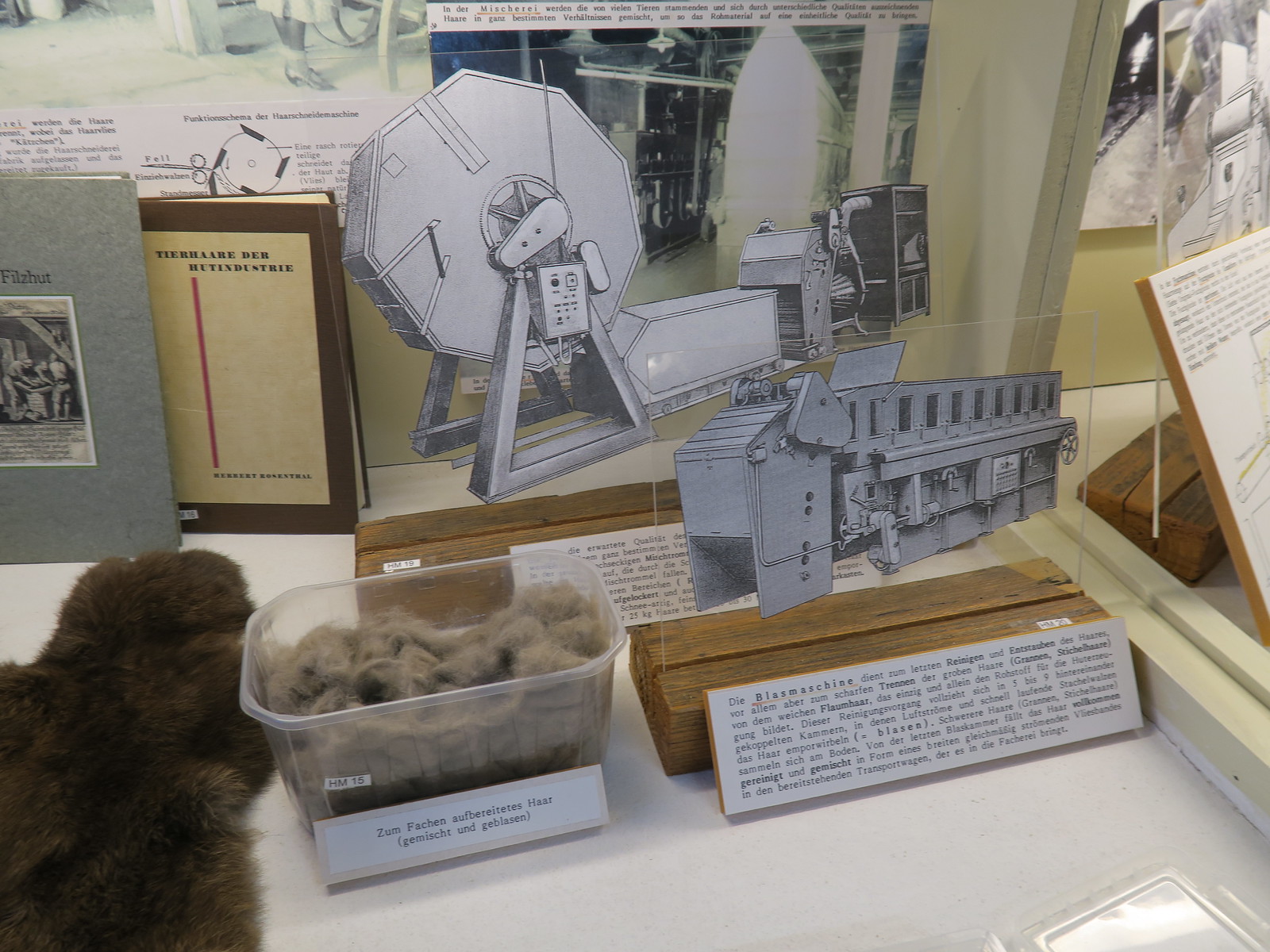
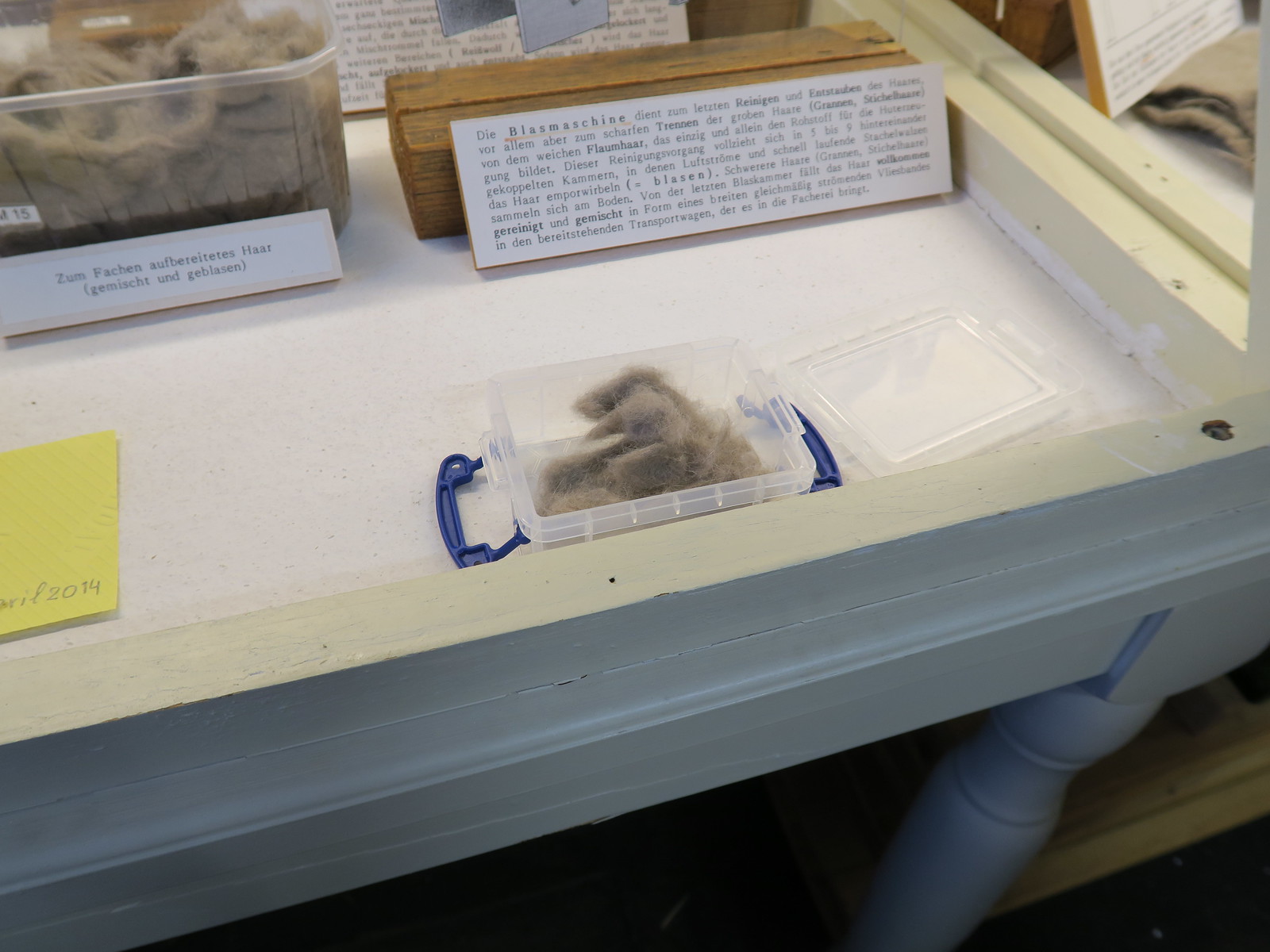
Trimmed hair (mixed and blown) (left side caption HM 15)
The blowing machine is used last Cleaning and dusting the hair, but especially for sharply separating coarse hair (bristle, prickly hair) from the soft downy hair, which is the sole raw material for making hats. (right side caption HM 20)
This cleaning process is full in 5 to 9 consecutively coupled chambers, in which air currents and fast-running spiked rollers blow up the hair (= blow). Heavier hair (bristle, prickly hair)
collect on the ground. From the last blow chamber the hair falls completely cleaned and mixed in the form of a wide uniformly streaming in the ready transport car, which brings it to the Facherei / Folding Department. (right side caption HM 20)
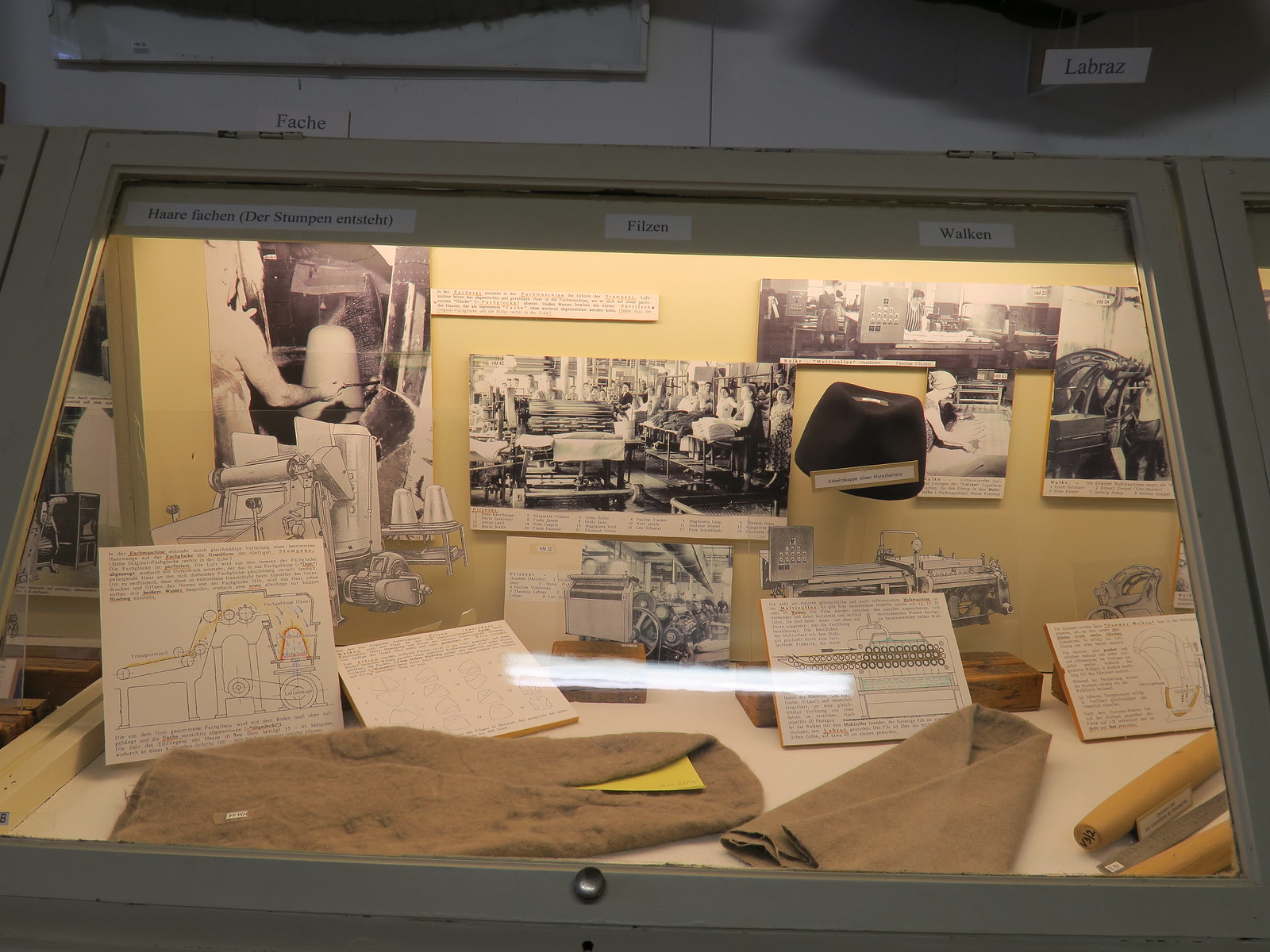
Fache / Forming
Hair Forming, Felting, Fulling
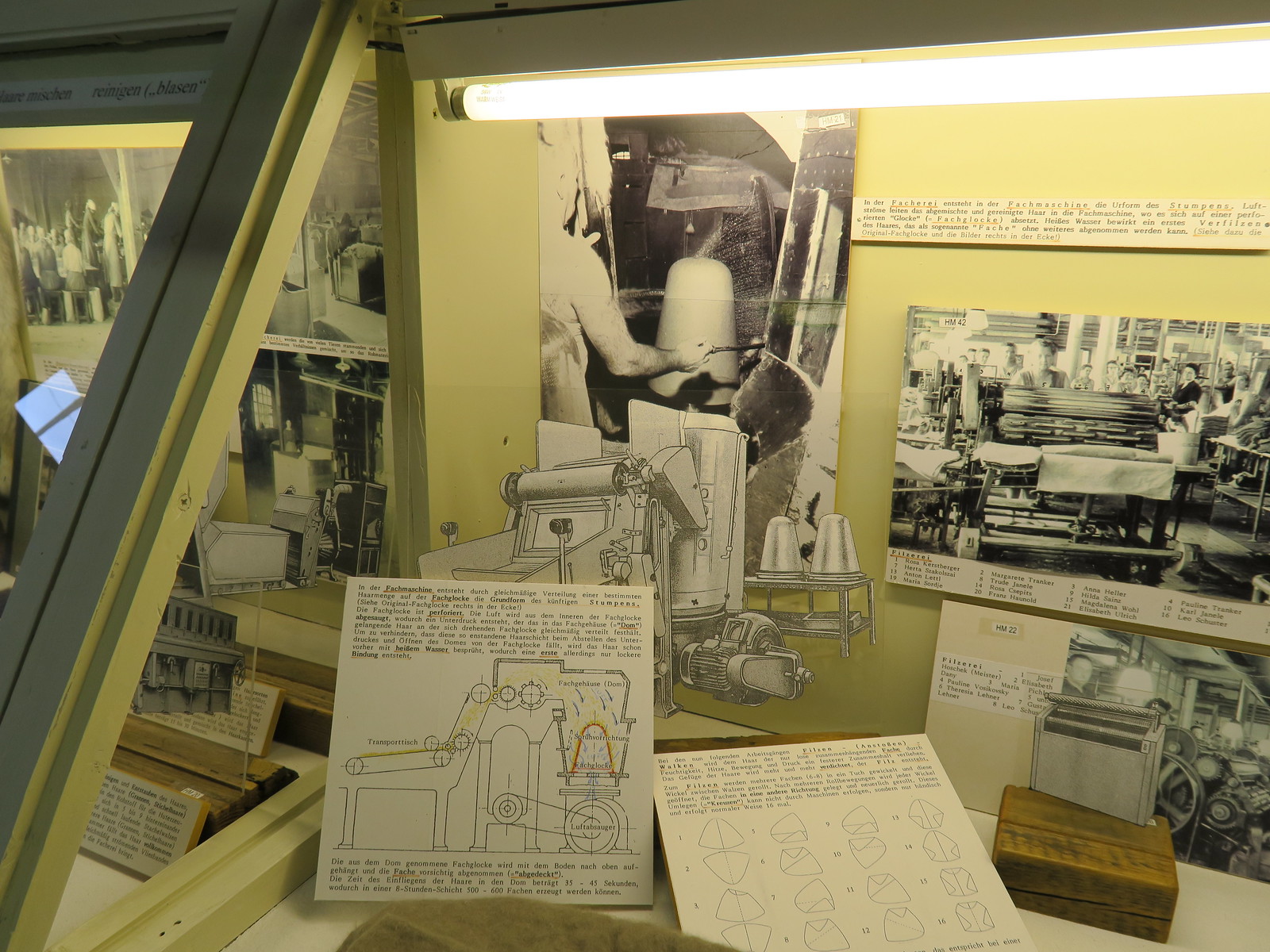
In the specialized machine, arises by uniform distribution of a particular
Amount of hair on the tray bell the basic shape of the future Stumpens.
(See original box on the right in the corner!)
The compartment bell is perforated. The air is coming from inside the compartment bell
sucked off, creating a negative pressure, which in the compartment housing (= "Dome")
reaching hair adheres to the rotating tray bell evenly distributed.
In order to prevent this hair layer thus obtained from
pressure and opening the dome falls from the box, the hair is already sprayed
before with hot water, making a first, however, only loose
binding arises. (far left diagram caption)
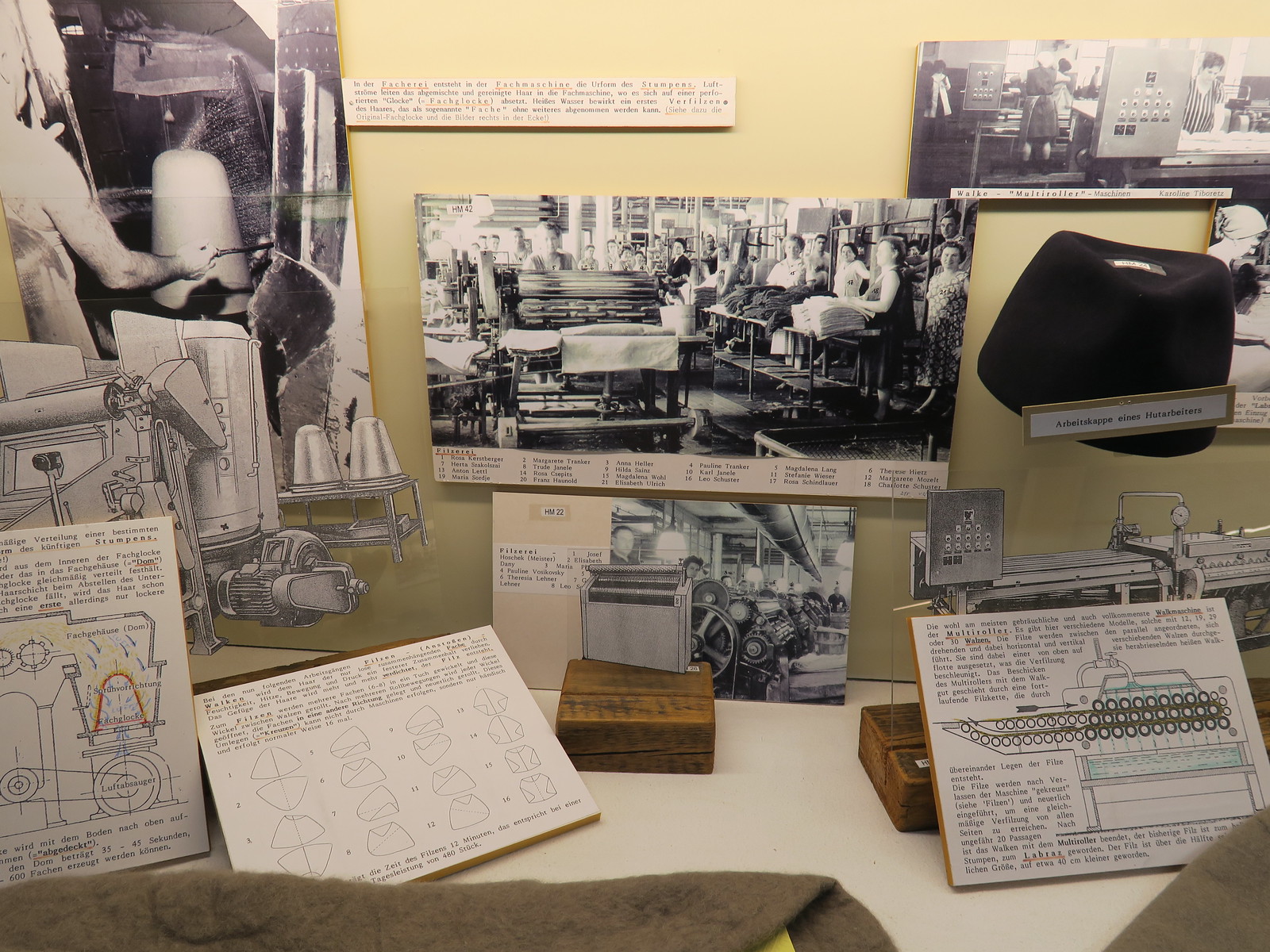
Felting Department Personal (HM 42, HM 22)
Probably the most common and also the most complete walke / fulling machine is the Multiroller. There are several models here, those with 12, 19, 29 or 30 rollers. The felts graze through between the parallel arranged rotating and horizontally and vertically shifting rollers. They are exposed to a hot water flow, which accelerates the felting. The feeding of the multirollers with the wrought material is done by a continuous felt chain, which is created by superimposing the felts. The felts graze after leaving the machine (see 'Felting') and reintroduced to achieve uniform coverage on all sides. After about 20 passages, the walking / fulling is finished with the multiroller, which ..... (lower right corner caption)
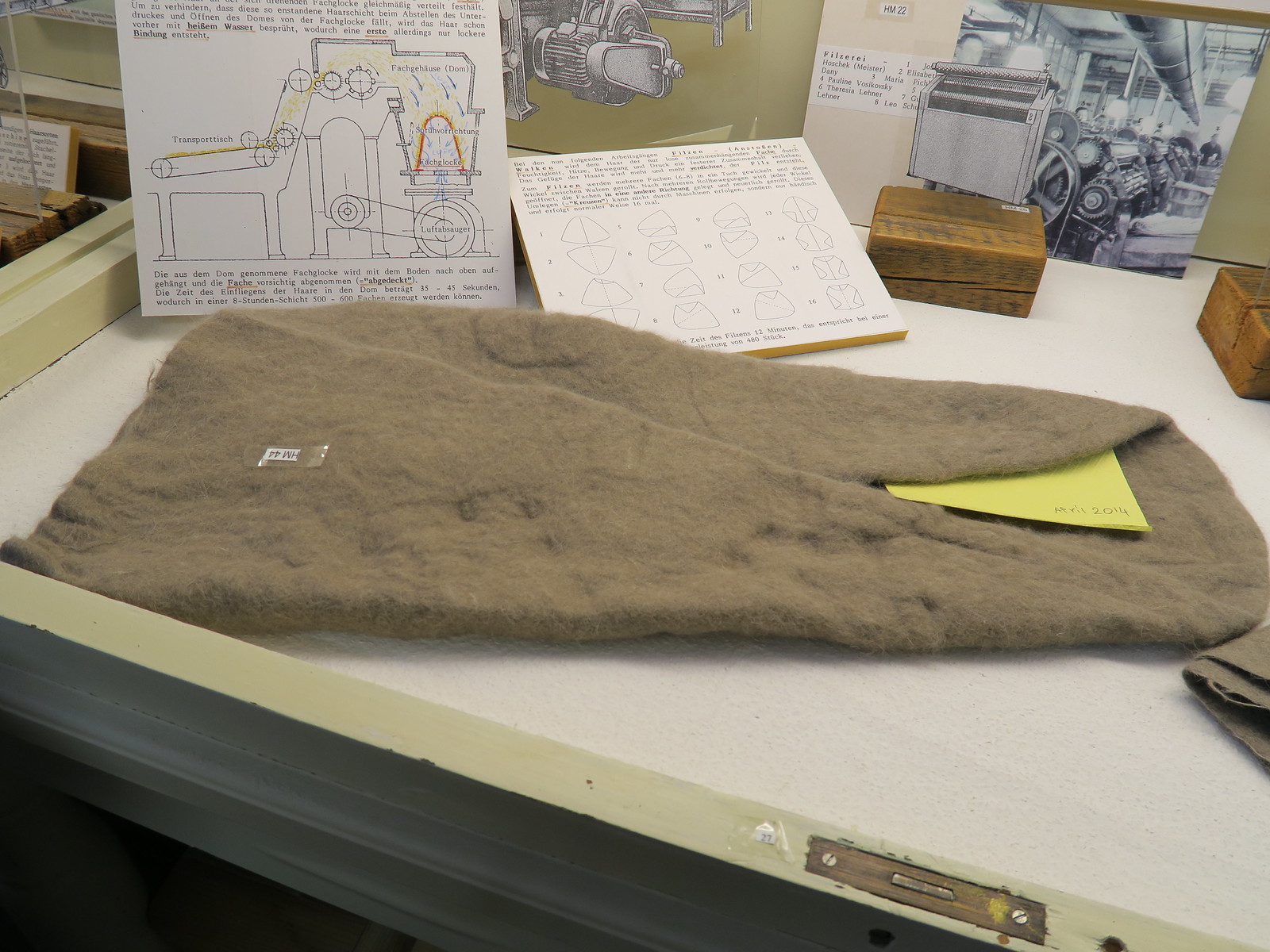
In the following work-style felts - (tossing) walking / fulling, the hair is given a firmer cohesion by moisture, heat, movement, and pressure.
The structure of the hair is compressed more and more, the felt arises. (center diagram caption)
For felting several compartments (6-8) are wrapped in a cloth and this
Rolls rolled between rollers. After several roll movements each roll becomes
opened, the subjects laid in a different direction and rolled again. This
Shifting ("crossing") can not be done by machines, but only by hand
and normally happens 16 times. (center diagram caption)
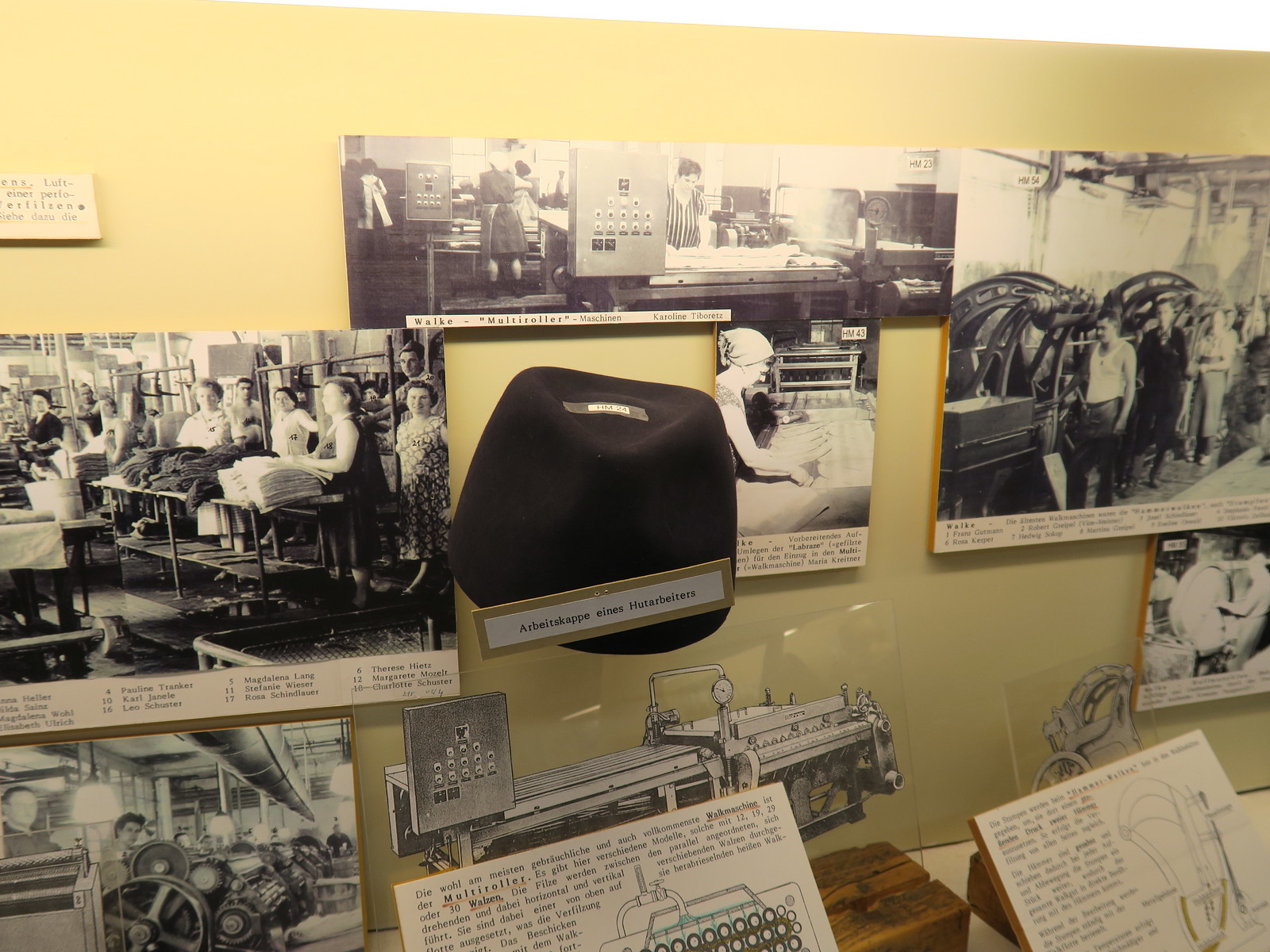
Walking / Fulling - Multi Roller Machine (HM 23, HM 43)
Workers Cap (center caption)
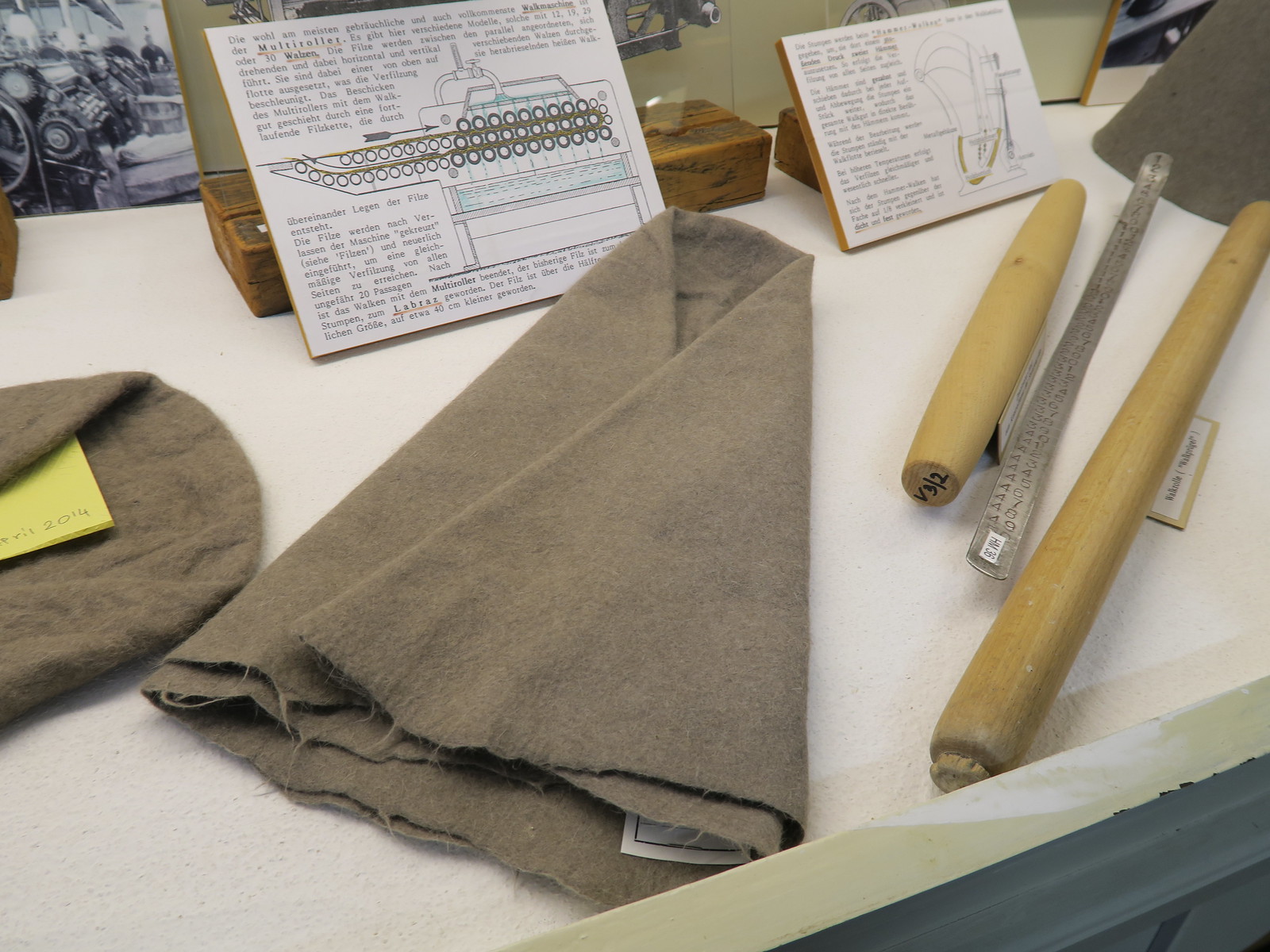
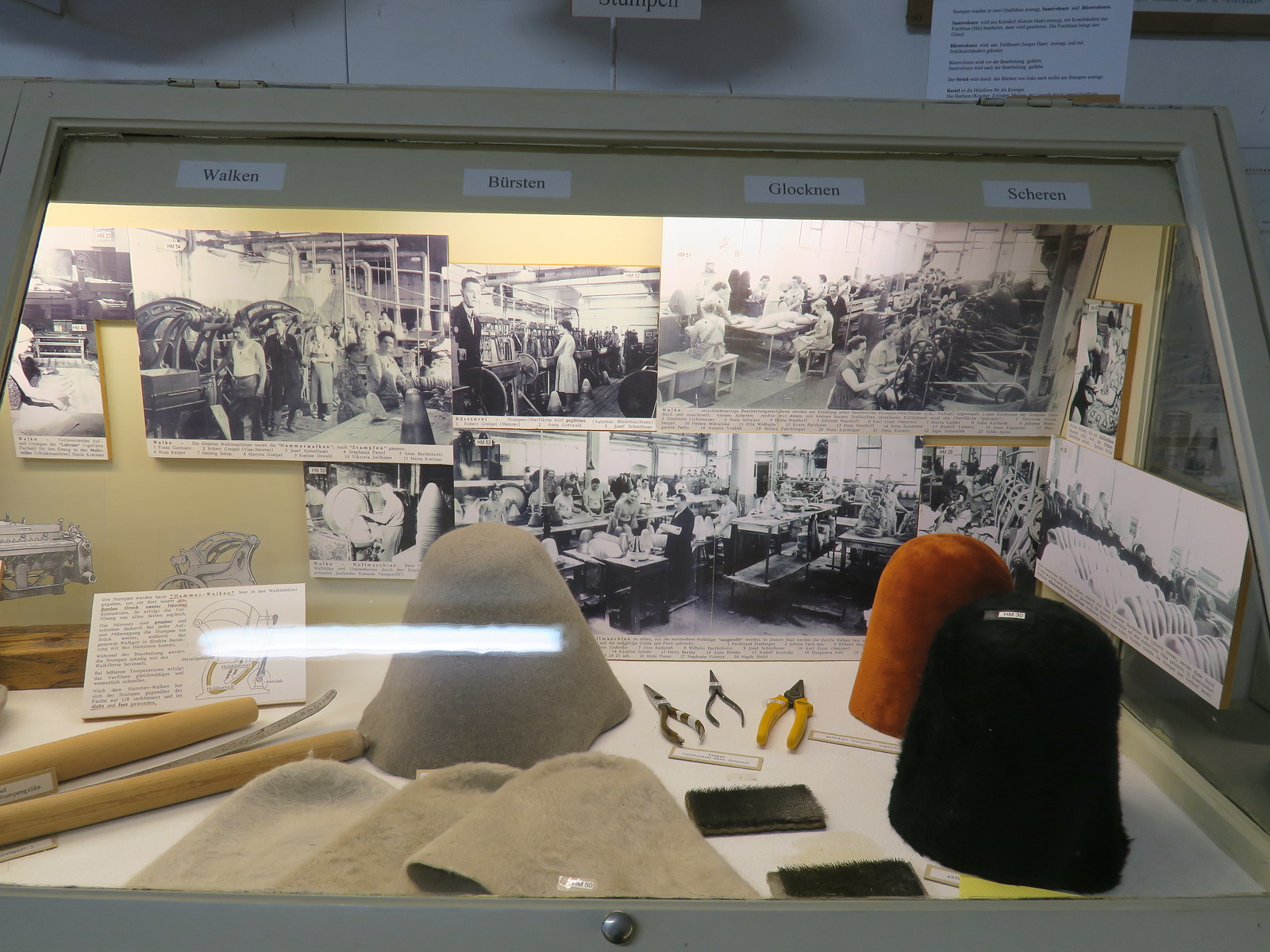
Fulling, Brushing, Touring, Clipping
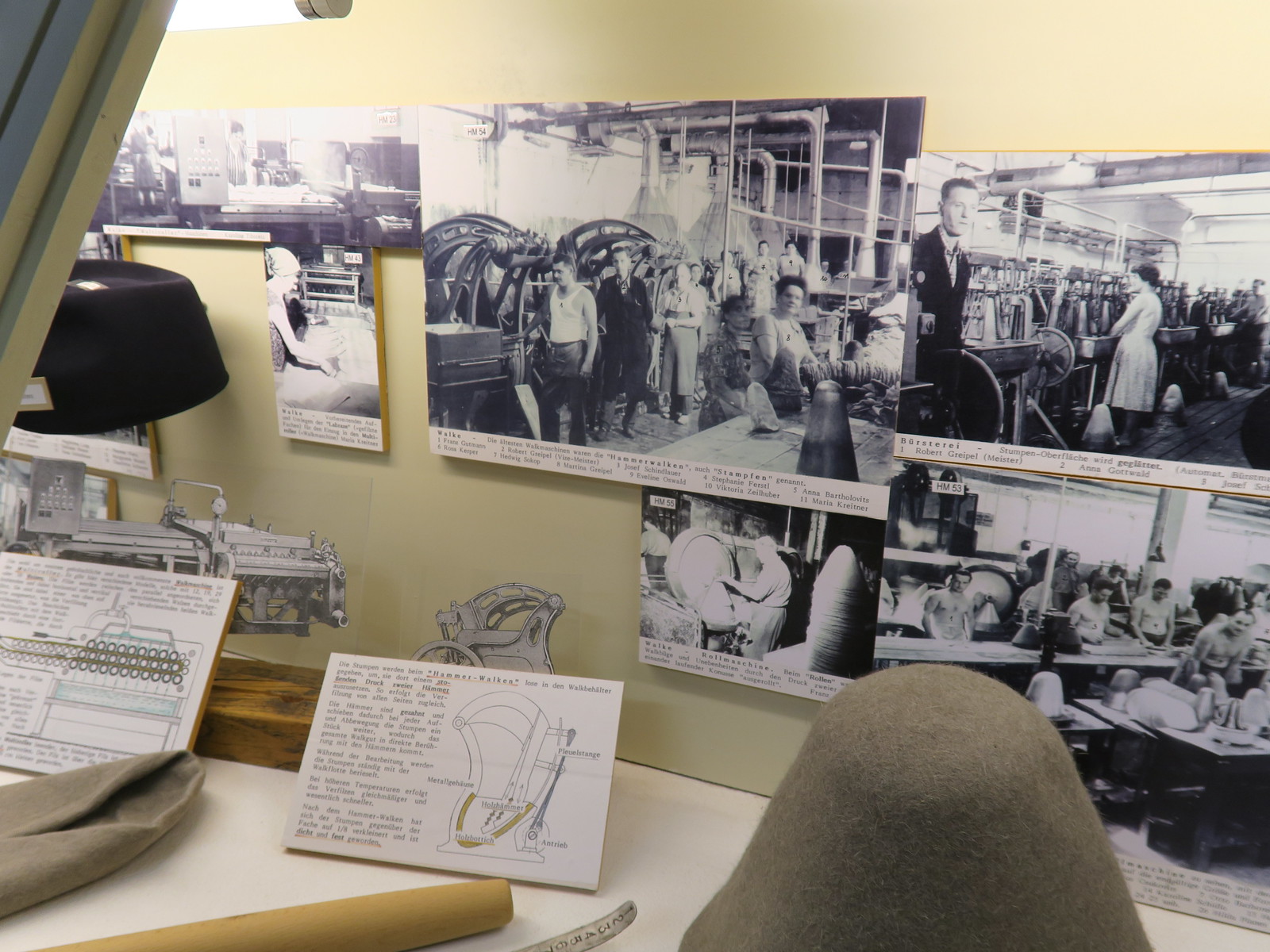
The stumps are loosely placed in the walker / fulling holder during "hammer walking / fulling" to expose them to a pushing pressure from two hammers. Thus, the felting takes place from all sides at the same time. The hammers are toothed and push the stumps a little further with each up and down excursion, so that the entire material to be drilled comes into direct contact with the hammers.
During processing, the stumps are constantly sprinkled with the Fulling water.
At higher temperatures felting occurs more uniformly and much faster. After the Hammering Walken / Fulling the stump has shrunk compared to the compartment to 1/8 and is dense and firm. (lower center diagram)
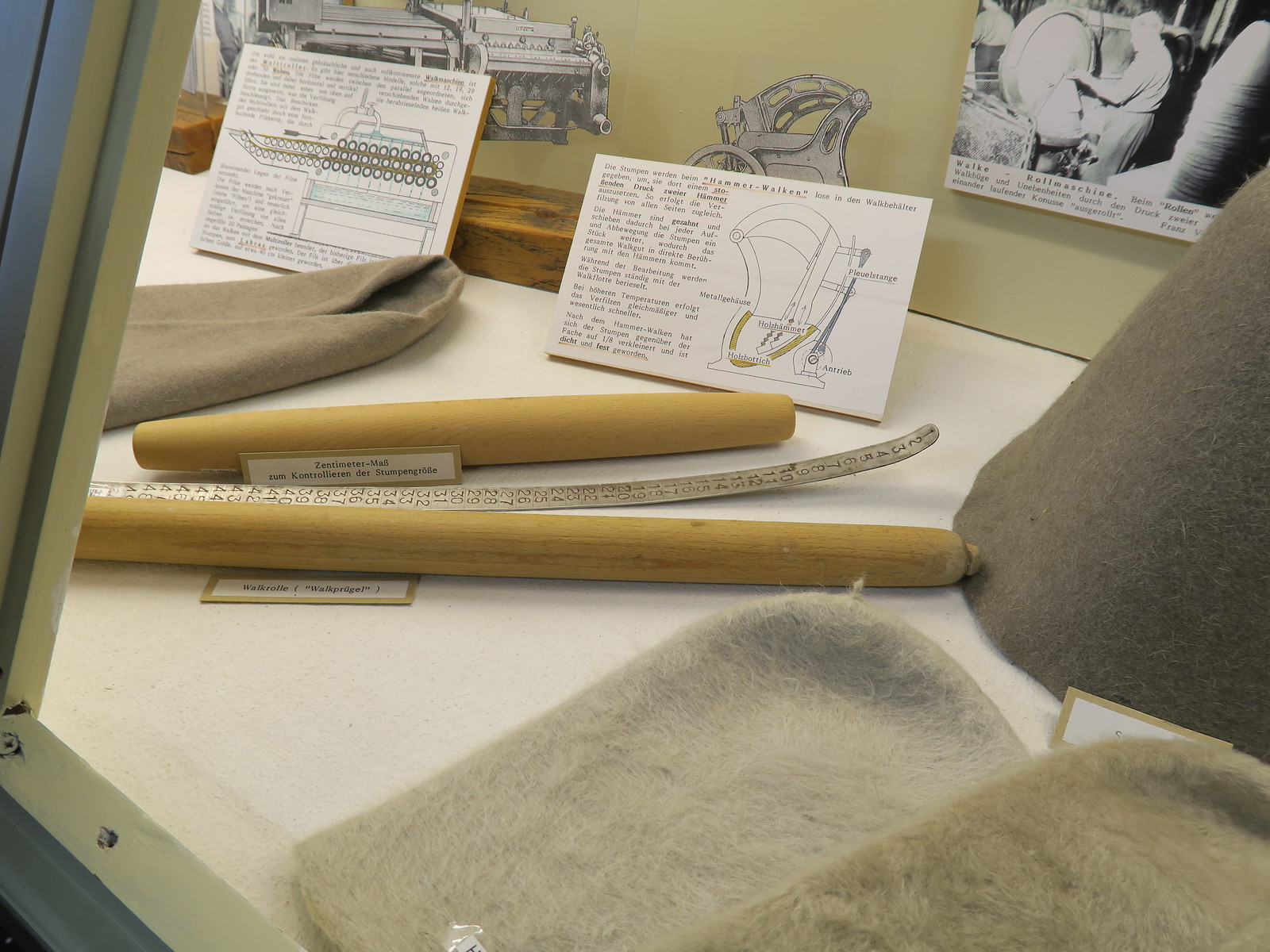
Centimeter measure to check the size of the stump.
Fulling Roll ("Fulling Beater")
Velour Stumpen / Hoods, Automatic Hot Wet Brushed (lower right corner)
Last edited: